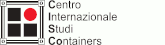
|
COUNCIL OF INTERMODAL SHIPPING CONSULTANTS | ANNO XXII - Numero 8/2004 - AGOSTO 2004 |
Industria
La fornitura delle linee di assemblaggio delle automobili
La VWT (Volkswagen Transport) è un grande gestore di trasporti secondo ogni parametro. Il suo personale consistente in 1.585 dipendenti movimenta complesse attività di trasporto, logistica ed approvvigionamento presso la sede centrale tedesca della società a Wolfsburg ed i suoi uffici decentrati in tutti i continenti. Essi gestiscono il flusso di materiali e veicoli per tutti i marchi del Gruppo Volkswagen (Volkswagen, Audi, Skoda e Seat) da 15 località di tutto il mondo. La VWT si aspetta di movimentare 163.100 TEU quest'anno nei traffici tra Europa, Asia ed Americhe, come mostra la tabella.
FLUSSI ANNUI DELLA VOLKSWAGEN TRANSPORT
PREVISTI PER IL 2004 |
Origine |
Destinazione |
Volumi annui (TEU) |
Europa |
U.S.A. |
9.000 |
Europa |
Messico |
12.700 |
Europa |
Sudamerica |
18.000 |
Europa |
Sudafrica |
16.000 |
Europa |
India |
8.900 |
Europa |
Cina |
75.000 |
U.S.A. |
Europa |
700 |
Messico |
Europa |
3.900 |
Sudamerica |
Europa |
4.100 |
Sudafrica |
Europa |
5.500 |
India |
Europa |
0 |
Cina |
Europa |
9.300 |
Totale |
|
163.100 |
Fonte: Volkswagen Transport
|
Questi volumi non sono solo grandi, ma anche complessi, come spiega Detlev Wollert, direttore trasporti marittimi ed aerei della VWT: "Un'auto adesso presenta approssimativamente 2.000 parti, e collateralmente esistono migliaia di loro permutazioni. La tendenza verso la personalizzazione delle auto ha reso le procedure della catena delle nostre forniture molto più complesse ed esigenti. E la riduzione dei tempi dei cicli è sempre più importante".
Kerstin Bergqvist, dirigente del settore contrattazioni nell'area mediterranea della Volvo Logistics, riecheggia questa opinione: "Noi movimentiamo migliaia di diverse componenti per i nostri clienti interni ed esse possono essere spedite in kit di montaggio ovvero come carichi containerizzati di particolari componenti. Tutte le possibilità e tutti i diversi instradamenti ingenerano una notevole complessità".
La Volvo Logistics movimenta approssimativamente 50.000 containers all'anno. Essa movimenta tutti i flussi delle componenti e dei veicoli finiti per le attività camion e bus del Gruppo Volvo. Essa movimenta altresì le componenti ed i veicoli della società Volvo Auto e due degli altri marchi della società Ford Motor in Europa. Le principali fabbriche della Volvo sono in Svezia, Belgio, Stati Uniti e Brasile e ha inoltre diversi impianti di assemblaggio in tutto il mondo. Come spiega Wollert, questa complessità viene affrontata in primo luogo con un'accurata programmazione: "Il punto di partenza alla Volkswagen è una stretta collaborazione in fase di programmazione tra tre diversi settori: si tratta dell'impianto ricezione, del dipartimento auto smontate (CKD) e noi della VWT".
Ognuno di questi partecipanti ha un ruolo diverso: l'impianto di ricezione prevede la domanda di componenti; il dipartimento CKD si occupa dell'approvvigionamento e del consolidamento di tutte le componenti in centri di raccolta-chiave e li appronta per il trasporto; la VWT, infine, porta le componenti dai fornitori ai centri di raccolta, seleziona i vettori in uscita, effettua le prenotazioni inerenti alle consegne e dispone il trasporto sino all'impianto di destinazione. L'attività di pianificazione copre tutto quanto, dalla programmazione tattica a breve termine di particolare flussi fino alla simulazione degli effetti delle nuove infrastrutture, quale la costruzione di nuovi impianti e lo sviluppo di nuovi centri di consolidamento.
Anche la Volvo Logistics sta molto vicina ai propri clienti. Dichiara Berqvist: "Siamo in costante dialogo con tutti i nostri clienti e parliamo con loro della possibilità di anticipare la domanda, discutendo la loro frequenza e le esigenze in termini di tempi di viaggio. Si tratta di un ambiente molto dinamico, in cui la domanda può mutare facilmente. Abbiamo bisogno di aiutare i nostri clienti ad adeguare i propri programmi di conseguenza". La Volvo Logistics dispone persino di proprio personale dislocato negli uffici di alcuni dei propri clienti per migliorare la reciproca comprensione ed il flusso delle informazioni.
I flussi sono adesso più complessi, dato che le linee di assemblaggio d'oltremare hanno cessato di ordinare kits CKD. Con questo metodo tutte le parti richieste per l'assemblaggio di tre automobili vengono imballate in un container da 40 piedi e spedite all'impianto di assemblaggio. La domanda di maggiori livelli di personalizzazione e l'aumento delle esigenze locali significa che l'approccio non è più appropriato. Invece, le componenti-chiave vengono spedite all'impianto di assemblaggio alla rinfusa, con volumi più elevati e meno componenti di valore reperite localmente. Questa nuova varietà incrementa in modo significativo la complessità dei compiti logistici, così come la necessità di un eccellente coordinamento tra tutte le parti coinvolte.
Il procedimento giorno per giorno alla Volkswagen comincia dall'impianto di ricezione che inoltra un ordine di acquisto ad un fornitore. Quando i prodotti sono pronti, la VWT provvede alla raccolta presso il fornitore ed alla consegna al centro CKD appropriato, laddove le componenti vengono preparate per la spedizione e consolidate. Il centro CKD invia una lista d'imballo alla VWT, che quindi effettua la prenotazione presso la linea di trasporto. La VWT provvede al prelievo del contenitore vuoto presso il vettore ed al trasporto alla volta del centro di consolidamento, laddove viene riempito prima di essere consegnato al vettore per la spedizione. La VWT riceve altresì una domanda con preavviso di quattro settimane da ciascun centro di consolidamento al fine di agevolare la programmazione. La VWT movimenta tutte le procedure di trasporto a destinazione e la consegna finale all'impianto di ricevimento.
Berqvist è stato molto chiaro in ordine a che cosa la Volvo Logistics richiede ai propri vettori: "Affidabilità, frequenza e precisione sono i criteri-chiave. Il vettore ha bisogno di capire che gli impianti dipendono da un flusso affidabile di componenti allo scopo di sostenere la produzione, di modo che vi è molto poco spazio per gli errori. Se un carico containerizzato di motori perde la nave programmata, la linea di assemblaggio potrebbe fermarsi. Dobbiamo evitare che questo accada".
Wollert - che in precedenza era alla Hapag-Lloyd e che perciò ha visto entrambi i lati dell'equazione - lamenta che ci sono voluti un bel po' di tempo e di sforzi per far sì che i vettori marittimi comprendessero l'importanza dell'affidabilità. Sostiene infatti: "Le parti di auto destinate ad una linea di produzione non sono come le altre derrate. Il ritardo di un carico containerizzato di birra potrebbe essere irrilevante, ma il ritardo di un solo contenitore di componenti di auto può essere un serio problema. Anche se manca una sola parte, non si può costruire l'auto".
(da: Containerisation International, giugno 2004)
|